Advanced Welding WPS: Customizing Specs for Complex Tasks
Advanced Welding WPS: Customizing Specs for Complex Tasks
Blog Article
Unlocking the Power of Welding WPS: Approaches for Effectiveness and Safety in Manufacture
In the world of fabrication, Welding Treatment Specs (WPS) stand as the foundation of welding operations, determining the essential actions for attaining both efficiency and safety and security in the construction process. Recognizing the ins and outs of WPS is paramount to using its complete capacity, yet several organizations battle to unlock real power that lies within these records (welding WPS). By delving into the strategies that optimize welding WPS, a globe of enhanced efficiency and increased security waits for those prepared to discover the subtleties of this vital facet of fabrication

Importance of Welding WPS
The value of Welding Treatment Specs (WPS) in the manufacture industry can not be overstated. WPS work as an essential roadmap that describes the needed actions to ensure welds are carried out regularly and appropriately. By specifying important specifications such as welding processes, materials, joint styles, preheat temperature levels, interpass temperature levels, filler steels, and post-weld heat treatment demands, WPS give a standard approach to welding that improves effectiveness, high quality, and security in manufacture procedures.
Adherence to WPS aids in achieving uniformity in weld quality, minimizing the likelihood of defects or structural failures. This standardization additionally helps with compliance with industry policies and codes, guaranteeing that produced structures satisfy the needed security requirements. Additionally, WPS documents makes it possible for welders to duplicate successful welding treatments, bring about regular results throughout various tasks.
Basically, the careful development and rigorous adherence to Welding Treatment Specifications are vital for upholding the integrity of welded frameworks, protecting versus prospective hazards, and promoting the online reputation of manufacture business for supplying top notch product or services.
Secret Aspects of Welding WPS

Enhancing Performance With WPS
When maximizing welding procedures, leveraging the crucial components laid out in Welding Procedure Specs (WPS) ends up being essential for simplifying procedures and making best use of productivity. One way to enhance effectiveness with WPS is by thoroughly choosing the suitable welding criteria. By sticking to the details standards given in the WPS, welders can guarantee that the welding devices is set up correctly, bring about high-quality and consistent welds. Additionally, following the pre-approved welding series described in the WPS can substantially lower the time invested in each weld, ultimately enhancing total efficiency.
Additionally, correct training and qualification of welders in understanding and carrying out WPS can better enhance efficiency. Ensuring that all employee are well-versed in interpreting and performing the WPS properly can rework and reduce mistakes, conserving both time and resources. Regularly assessing and upgrading the WPS to include any kind of lessons learned or technical developments can also add to efficiency renovations in welding procedures. By accepting the guidelines established forth in the WPS and constantly looking for means to enhance processes, makers can achieve greater efficiency degrees and remarkable end results.
Ensuring Safety in Manufacture
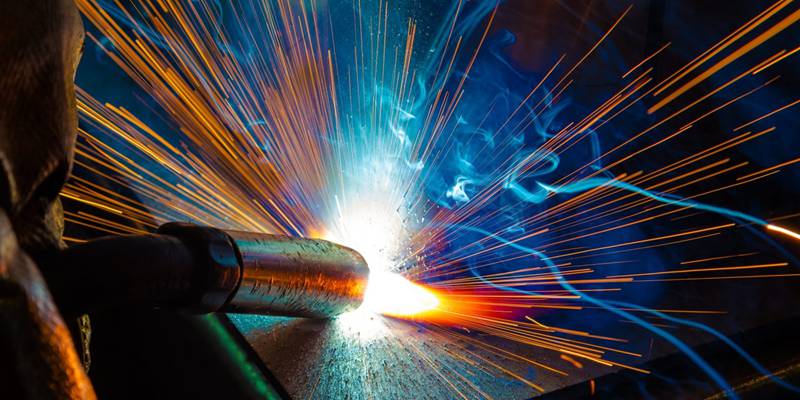
Security procedures in construction play a critical role in safeguarding personnel and enhancing operational procedures. Ensuring safety and security in manufacture involves a diverse method that encompasses various facets of the welding process. One Read Full Article fundamental aspect is the stipulation of personal safety devices (PPE) customized to the specific risks existing in the manufacture atmosphere. Welders need to be equipped with suitable gear such as headgears, handwear covers, and safety clothes to alleviate risks related to welding tasks.
Moreover, informative post adherence to correct air flow and fume removal systems is vital in maintaining a healthy and balanced work setting. Welding fumes contain dangerous compounds that, if inhaled, can present major health dangers. Implementing effective air flow procedures helps to minimize direct exposure to these unsafe fumes, advertising breathing health and wellness among employees.
Routine equipment maintenance and examinations are also necessary for ensuring safety and security in fabrication. Faulty equipment can result in accidents and injuries, emphasizing the value of regular checks and prompt fixings. By focusing on precaution and promoting a culture of awareness, fabrication centers can create a effective and safe and secure work atmosphere for their workers.
Carrying Out WPS Best Practices
To improve functional efficiency and make sure high quality outcomes in fabrication processes, incorporating Welding Treatment Specification (WPS) finest methods is vital. Choosing the ideal welding process, filler product, and preheat temperature defined in the WPS is vital for attaining the preferred weld quality. Making sure that qualified welders with the essential accreditations lug out the welding treatments according to the WPS guidelines is vital for consistency and reliability.
Conclusion
To conclude, welding WPS plays a vital duty in making certain effectiveness and safety in fabrication processes. By focusing on crucial elements, boosting effectiveness, and applying finest methods, companies can maximize their welding operations. It is important to prioritize precaution to stop crashes and ensure a smooth manufacturing process. By following these methods, services can open the complete capacity of welding WPS in their manufacture procedures.
In the realm of fabrication, Welding Procedure Requirements (WPS) stand as the backbone of welding operations, determining the required steps for achieving both efficiency important site and security in the fabrication procedure. By defining vital specifications such as welding processes, products, joint layouts, preheat temperature levels, interpass temperatures, filler metals, and post-weld warm therapy demands, WPS supply a standardized method to welding that boosts performance, top quality, and safety and security in manufacture procedures.
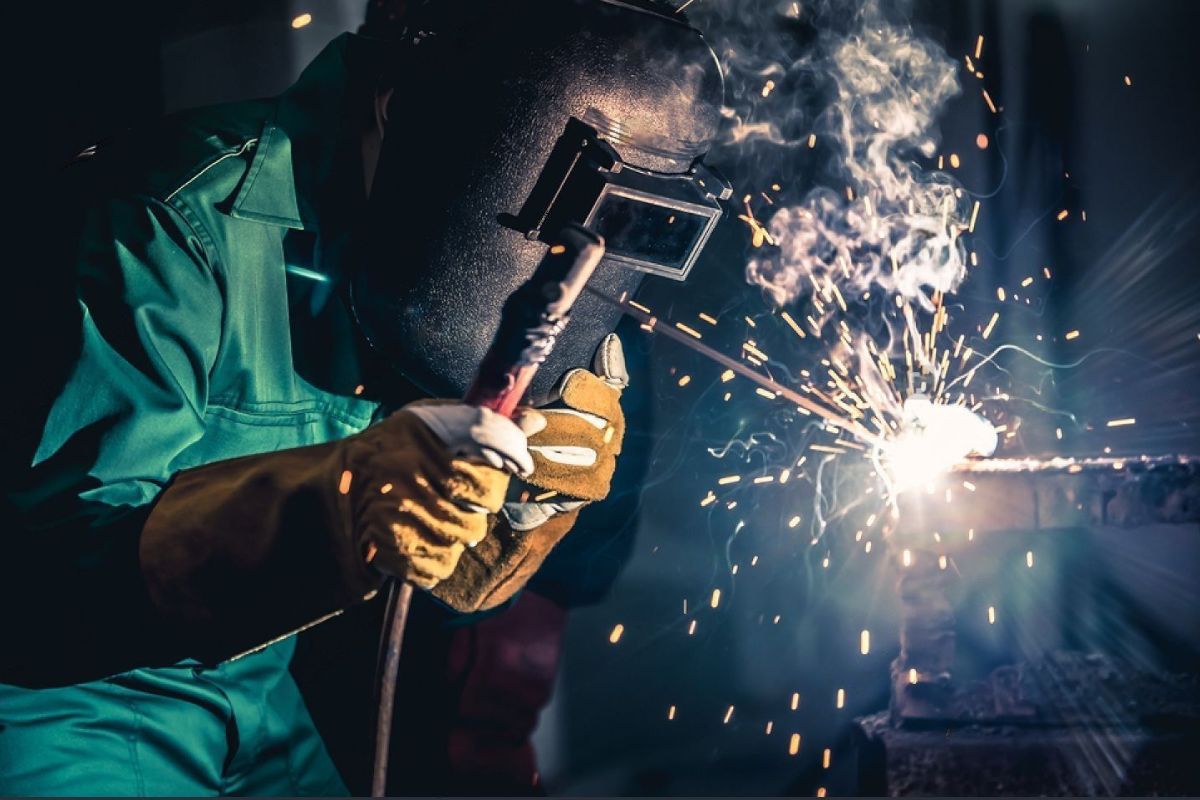
When optimizing welding procedures, leveraging the essential components outlined in Welding Treatment Specs (WPS) comes to be crucial for optimizing and improving processes efficiency. (welding WPS)
Report this page